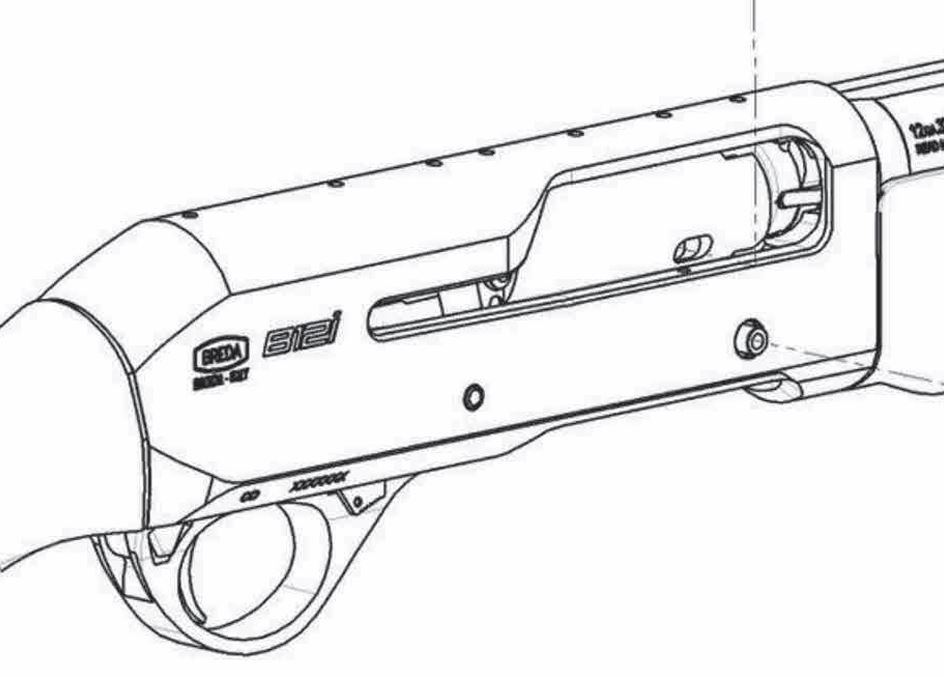
Bruno Civolani revolutionized the world of waterfowl when he developed his turn-bolt inertia system. Despite the core system remaining virtually unchanged for nearly a half century, it is shocking that many of its operators, some of which have used Civolani’s system since its inception, still know very little about how it actually operates. In this article, I will attempt to change that- class is now in session.
Bruno Civolani was not the first to develop the inertia system. The system was originally developed by Carl Axel Theodor Sjogren of Sweden circa 1900. His shotgun that first utilized an inertia system was marketed and sold as the “Normal Automatic: Sjogren System”. For the remainder of this article, I will simply refer to it as the “Sjogren”.

Photo credit: Engineering magazine, 6/14/1908
Developing an autoloading shotgun posed as a significant challenge for era. First and foremost, to this day shotgun shells are only standardized on rim and brass diameter, and overall length of the expanded shell. Nothing else about the shell is standardized. The shell’s overall length, the shot size, shot shape, wad, powder charge, powder composition, and even crimping are not standardized. Unlike centerfire and rimfire rifle rounds, the casing dimensions must fall within a certain tolerance in order to safely fire. One can take a round of 30-06 manufactured by Lake City, Norma in Norway, and PPU in Serbia, and expect to be able to safely chamber and fire in the same firearm and expect the same results. Shotgun shells are not so standardized. To compound the issue, black powder at this time would still be used in shotgun shells for another 20 years. Making matters even worse, shotshells come in all different sizes, shapes, powder charges, and shot weights, and shot sizes. According to SAAMI, there were over 4,000 different shotshell loads in 1926 alone.
So, how does one overcome the core problem of developing a gun that can safely fire and reliably cycle a majority of the myriad of shells on the market? John Browning solved this by utilizing a braking system composed of friction rings. Carl Sjogren on the other hand, utilized basic physics.
The inertia action’s core principal, as developed by Sjogren, utilizes the direct rearward motion of the entire firearm itself to cycle the action. Mr. Sjogren realized that by indirectly harnessing recoil, you could delay the opening of the action just long enough for the chamber pressure to drop within safe levels to begin the extraction stroke via a simple compression spring, while still being able to handle a majority of different shells. While the speed of compression and recoil may change with the load of the shell, the time it takes to unlock the action does not.
The inertia system is actually remarkably simple for its time, and even as a generation-1 firearm, and its core function has remained virtually unchanged for over a century. The core system is composed of only 4 components: a locking bolt, a bolt carrier, a very stout inertia spring, a recoil spring. The key to this system being the inertia spring.

Photo credit: Engineering magazine, 6/14/1908
The inertia spring is sandwiched between the locking bolt and the bolt carrier. As the locking bolt itself is locked into the firearm, the bolt will move rearward under recoil with the gun. The bolt carrier, however, is floated between the inertia spring and the recoil spring, and is generally free to move about with enough force. It is only held inside guide rails to limit its movement into only one plane of motion. As the gun recoils, the bolt moves rearward, but the bolt carrier remains still. Remember Sir Isaac Newton’s laws of physics:
1. An object at rest remains at rest, and an object in motion remains in motion at constant speed and in a straight line unless acted on by an unbalanced force.
2. The acceleration of an object depends on the mass of the object and the amount of force applied.
3.Whenever one object exerts a force on another object, the second object exerts an equal and opposite on the first.
As the bolt travels rearward with the entire firearm against the resting bolt carrier, the inertia spring sandwiched between the two is compressed by the rearward motion. The spring then decompresses, and sends the bolt carrier rearward, unlocking the action and cycling the gun. High-speed footage of the process can be viewed below.
As most shotgun shells burn at relatively low pressure (typically under 14,000PSI), it is only a fraction of a second before the chamber pressure drops to a safe level for extraction after the shell is fired. Developing a straight blowback shotgun would require either an incredibly massive and heavy bolt, recoil springs too heavy to manually operate, or a combination of both, all of which would only be tuned for a single loading and thus not economically viable.
Sjogren’s system utilizes all of the laws of physics in a single stroke. By controlling the rate at which the action is unlocked, regardless of the shell, Sjogren effectively eliminated the need to manually tune the system for different shells, unlike Browning’s design. Bruno Civolani would later discover the Sjogren while apprenticing under gunsmith Orlando Grandi. and incorporate its mechanical principals into his now ubiquitous system.
The inertia system is not without its drawbacks. Being that its ability to cycle is based directly off the shell’s power, the shell must have sufficient power in order to reliably cycle the action. The inertia spring’s tension is a fixed component, and if it is not fully compressed, the action will not reliably cycle. As such, most inertia guns struggle with light target and clays loads. The physical weight of the gun itself also plays a role into cycling. If the shell cannot move the gun enough to compress the inertia spring, it will not cycle. A 6lb inertia gun will generally be able to cycle a lighter load than a 7lb inertia gun of the same gauge due to its weight alone. This is also why many sub-gauge inertia shotguns and even centerfire inertia rifles do not exist or are incredibly scarce; lighter recoiling cartridges, like .410, 30-06, 8x57, etc simply do not reliably generate enough recoil to reliably cycle an inertia system.
Additionally, one of the quirks of the inertia system comes into play with how the user holds the gun. As the entire gun needs to move in order to cycle the action, it is entirely possible to hold the gun too tightly in the shoulder with light target loads and manually induce a short stroke. We often see this in the industry with people switching from a pump or gas gun to inertia, where they have been taught to hold the gun very tightly. This is true for gas and recoil-operated guns: they must be held tightly in order to cycle. The opposite is true with inertia guns.
On the other hand, one of the main benefits to the inertia system is its ability to handle a wide variety of different loads with no mechanical changes to the firearm. A 3.5” supermagnum inertia gun can be fed waterfowl loads, turkey loads, home defense buckshot, and most target loads of sufficient power without changing a single part of the gun. With a 3.5” gas gun, meanwhile, will struggle with most target loads, and even some 3” magnum loads. The firearm would have to be modified to cycle these lighter loads. However, the firearm cannot now cycle 3.5” supermagnums in its light load configuration without causing significant damage to the firearm. The user would have to be conscious of what configuration the gun is versus what load they want to shoot- much like the Browning Auto-5.
The second benefit of the inertia system is is ease of maintenance. In Civolani’s design, there are only 15 components in the core action, and most of these are inside the bolt carrier group. For comparison, an AR-15, which is renowned for its simplicity, has 23 parts in its core action (including recoil and gas components). A gas gun requires consistent maintenance for keep it performing up to snuff. An inertia gun meanwhile, requires very little maintenance, and can handle quite a lot of abuse. Should a gas gun be submerged in water, one has to worry about water getting into the gas port, piston assembly, recoil assembly, and so forth. With an inertia gun, one just has to worry about draining the barrel. If the springs are not stainless, they should be at minimum oiled within a few days to prevent corrosion.
The Sjogren was sadly not particularly a successful shotgun. Production ceased in 1909, with only around 5,000 units built. As they are incredibly scarce in the United States particularly, I have never had my hands on one. I can imagine, however, it would be quite jarring for shooters of the era to have the mass of the sliding action coming rearward towards the shooter’s face. This may have been one of the reasons it was unsuccessful, but this is only speculation. Ian McCollum has a fantastic video on shooting the Sjogren, which can be viewed below.
Rus Hinkle
Banshee Brands Lead Gunsmith
Comments